CNC Precision Machining Manufacturers: The Key to Quality Metal Fabrication
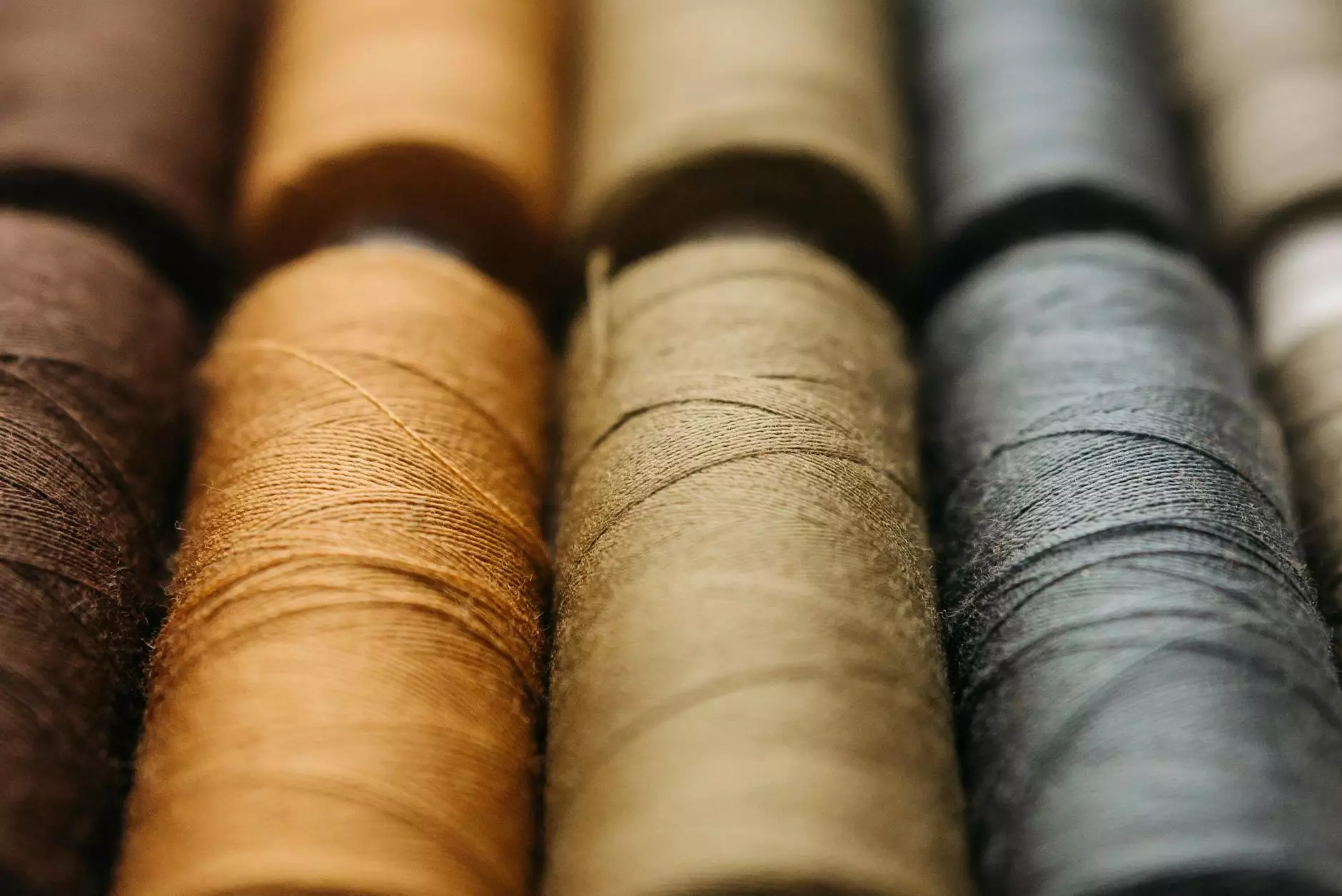
CNC (Computer Numerical Control) precision machining has become a cornerstone of modern manufacturing, significantly impacting the metal fabrication industry. As industries continue to evolve, the demand for precision and efficiency grows. Hence, cnc precision machining manufacturers play a vital role in fulfilling these needs by providing high-quality components with unparalleled accuracy.
The Role of CNC Precision Machining in Metal Fabrication
Understanding the importance of cnc precision machining starts with acknowledging its role within the broader context of metal fabrication. CNC machining allows for the automated control of machining tools, leading to numerous benefits:
- Increased Accuracy: CNC machines can produce intricate parts with tolerances as tight as a few microns, far surpassing human capabilities.
- Enhanced Efficiency: These machines can operate continuously, producing a significant volume of parts in a fraction of the time it would take manually.
- Consistency: Once a design is programmed, CNC machines can produce identical parts repeatedly without variation.
- Flexibility: CNC machining allows manufacturers to switch from one part design to another with minimal downtime, adapting to changing demands.
The Process of CNC Precision Machining
CNC machining involves several key steps, starting from design to the final product:
1. Designing the Prototype
It all begins with a digital design or a CAD (Computer-Aided Design) model of the component. This 3D model provides a detailed framework for what the final part should look like.
2. Programming the CNC Machine
The CAD model is translated into a G-code, which is a set of instructions that guides the CNC machine on how to operate. This code contains essential details about feeds, speeds, and tool movements.
3. Material Selection
Choosing the right metal material is crucial for the success of the machining process. CNC precision machining manufacturers work with a range of materials including:
- Aluminum
- Stainless Steel
- Copper
- Titanium
4. Machining Process
The CNC machine does its work by following the programmed G-codes to cut, shape, and form the metal material into the desired part. This may involve processes like:
- Milling
- Turning
- Drilling
- Grinding
5. Quality Control
Once the machining process is complete, quality control checks are performed to ensure that the parts meet the required specifications and tolerances. This critical step distinguishes leading cnc precision machining manufacturers from the competition.
Advantages of Partnering with CNC Precision Machining Manufacturers
Engaging with reputable cnc precision machining manufacturers like Deep Mould provides several advantages:
- Expertise: These manufacturers often have years of experience and extensive knowledge about materials, tooling, and machining processes.
- Cutting-Edge Technology: Leading CNC manufacturers utilize the latest technology and machinery, enhancing accuracy and efficiency.
- Cost-Effectiveness: By producing high-quality parts quickly, businesses can save time and money while minimizing waste.
- Support and Consultation: Many manufacturers offer design assistance and consultation services to help businesses choose the right materials and processes.
Industries Benefiting from CNC Precision Machining
The reach and applications of cnc precision machining extend across various industries:
- Aerospace: The aerospace sector demands parts that meet stringent safety and performance standards, which CNC machining can deliver.
- Medical Devices: Precision is critical in the production of medical devices; CNC machining provides the required accuracy.
- Agricultural Equipment: CNC machining is vital for producing robust parts that can withstand the rigors of agricultural work.
- Automotive: The automotive industry relies heavily on precision parts for engines, chassis, and other components.
Choosing the Right CNC Precision Machining Manufacturer
Not all manufacturers are created equal. Here are key factors to consider when choosing a cnc precision machining manufacturer:
1. Experience and Expertise
Look for manufacturers with a proven track record and extensive experience in the specific industry you are targeting.
2. Technology and Equipment Quality
Assess the technology and equipment types they use. Advanced machinery often translates into better quality and efficiency.
3. Quality Assurance Practices
Inquire about their quality control processes. A strong commitment to quality assurance is crucial for delivering reliable products.
4. Customer Service
Good communication and customer service are essential for a smooth partnership. Ensure the manufacturer is responsive and willing to engage with you.
The Future of CNC Precision Machining
The industry is experiencing rapid advancements through innovations in robotics, AI, and machine learning. These technologies are set to transform the world of cnc precision machining by:
- Improving Efficiency: Automation will further streamline production processes.
- Enhancing Customization: AI-driven designs will allow for highly customized production runs without significant delays.
- Reducing Errors: Smart systems can alert operators to anomalies in the machining process in real-time.
Conclusion
In conclusion, cnc precision machining manufacturers are pivotal in driving the metal fabrication industry towards efficiency, quality, and innovation. As we look to the future, the role of these manufacturers will only continue to grow and evolve, making them invaluable partners for businesses looking to succeed in an increasingly competitive landscape.
For best-in-class machining solutions that meet diverse industrial needs, partnering with a seasoned manufacturer like Deep Mould ensures you benefit from advanced technology, expert knowledge, and a commitment to quality.