Understanding Prototype Mold Makers Manufacturers
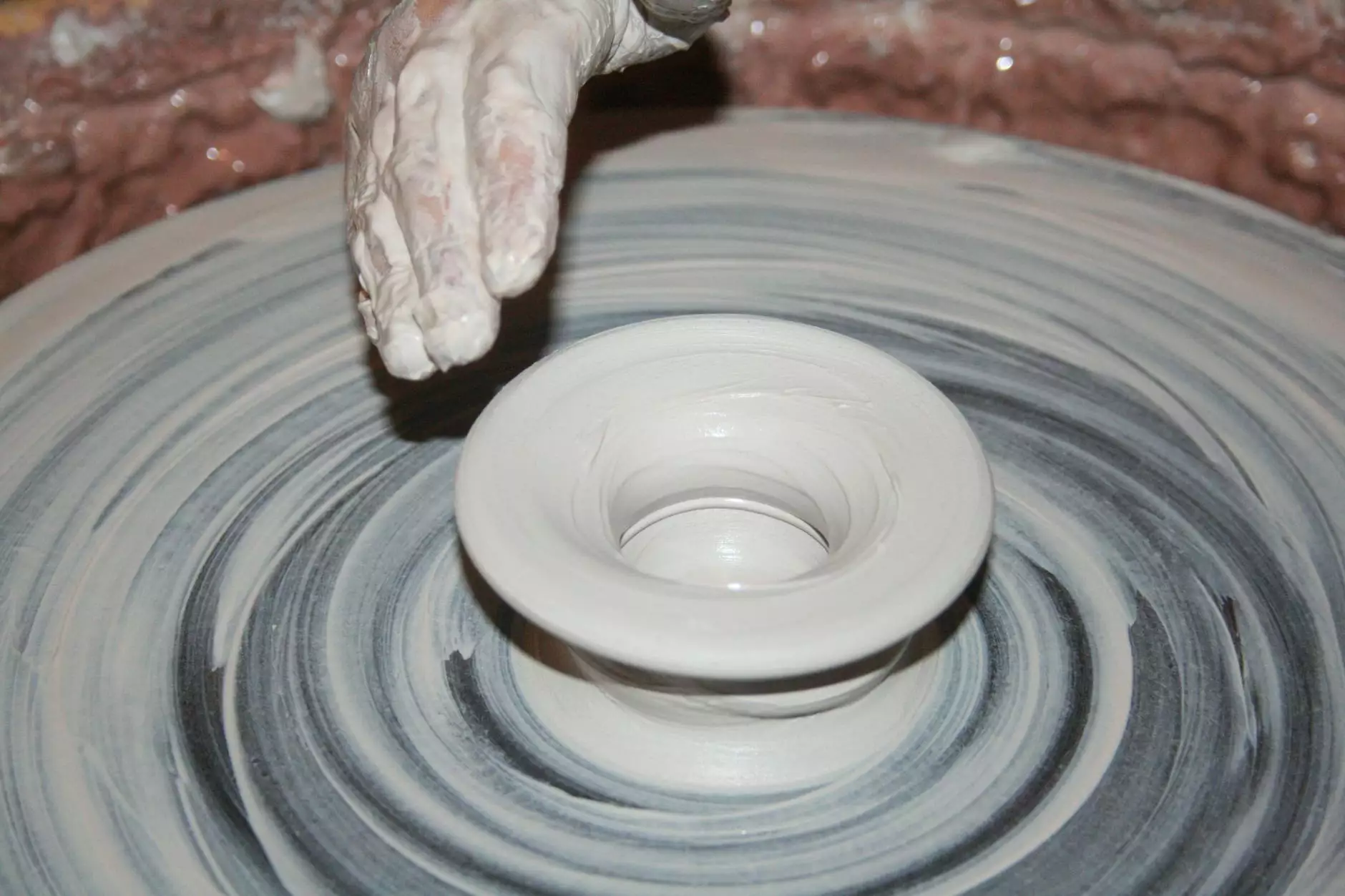
In the ever-evolving landscape of manufacturing, prototype mold makers manufacturers play a pivotal role in bridging the gap between concept and reality. The demand for high-quality, precise metal components necessitates molds that can accurately replicate designs with utmost fidelity. This detailed exploration delves into the nuances of mold making, the significance of prototype molds, and how they influence the field of metal fabrication.
The Significance of Prototype Mold Making
Prototype mold making is a crucial step in the product development process. It allows manufacturers to create a physical version of their product before full-scale production. This process is essential for several reasons:
- Design Validation: Prototypes enable designers to test form, fit, and function, ensuring the final product meets expectations.
- Cost Efficiency: Identifying design flaws in the prototype stage reduces costs associated with mass production errors.
- Faster Time to Market: Quick prototyping accelerates the product development cycle, allowing businesses to respond promptly to market demands.
Choosing the Right Prototype Mold Makers Manufacturers
Selecting the right prototype mold makers manufacturers involves a thorough evaluation of several factors. Here are key considerations:
Expertise and Experience
The manufacturer's experience in creating prototypes for various industries is crucial. Look for firms that have a proven track record and testimonials from clients in your field.
Technology and Techniques
Modern mold making requires advanced technologies such as CNC machining, 3D printing, and CAD software. Manufacturers should invest in state-of-the-art equipment to ensure precision and efficiency.
Material Selection
The quality of the mold material directly affects the prototype's durability and performance. Top manufacturers will offer a range of materials such as:
- Steel
- Aluminum
- Composite materials
Quality Assurance
Reputable manufacturers implement stringent quality control measures. Certifications like ISO 9001 can indicate a commitment to quality and reliability.
The Process of Prototype Mold Manufacturing
The process of creating a prototype mold consists of several stages, each vital to producing a high-quality product:
Concept and Design
The journey begins with a detailed design and specification of the product. In this phase, feedback from design teams and stakeholders is critical to refine ideas.
3D Modeling
Using advanced CAD software, designers create a 3D model of the mold. This step allows for precise visualization and adjustments before physical production begins.
Mold Construction
Once the design is finalized, the actual mold is constructed. This phase can involve:
- CNC Machining: For precise shaping of mold components.
- 3D Printing: For creating complex geometries that traditional methods may struggle with.
Testing and Validation
Testing the prototype mold is crucial. This involves producing a few initial parts and analyzing them against design specifications to ensure quality standards are met.
Benefits of Using Prototype Mold Makers Manufacturers
By engaging with expert prototype mold makers, businesses can realize several benefits that significantly enhance their manufacturing processes:
Enhanced Innovation
Prototype molds foster a culture of innovation. Rapid iteration of designs encourages creative problem-solving and exploration of new ideas.
Reduced Risk
Testing prototypes minimizes the risk of costly production errors. Manufacturers can make necessary adjustments before committing to large quantities.
Improved Collaboration
Working with experienced mold makers enhances collaboration between manufacturers, designers, and engineers. This teamwork can lead to higher-quality output and more successful products.
The Role of Metal Fabricators in Prototype Mold Making
Metal fabricators are integral to the process of prototype mold making, providing the necessary expertise to work with metal materials effectively. Their skills are essential for:
- Welding: Creating strong joints between mold components.
- Machining: Shaping metal components to precise specifications.
- Assembly: Bringing together various mold parts into a cohesive unit.
Future Trends in Prototype Mold Making
The landscape of prototype mold making is constantly evolving. Several trends are shaping the future of this industry:
Increased Use of Automation
Automation is streamlining production processes, increasing accuracy, and reducing lead times. Automated machines can quickly produce complex molds with little human intervention.
Integration of AI and Machine Learning
Artificial Intelligence (AI) is being harnessed to predict design performance and optimize manufacturing processes. These technologies can lead to more efficient mold designs that anticipate potential issues.
Sustainability Measures
As industries become more eco-conscious, the demand for sustainable practices in mold making is rising. Manufacturers are exploring ways to reduce waste and use recyclable materials.
Conclusion
In conclusion, prototype mold makers manufacturers are essential in the manufacturing sector, particularly in the realm of metal fabrication. They enable the transformation of ideas into tangible products through meticulous design, innovative techniques, and a commitment to quality. By selecting the right manufacturers and understanding the mold-making process, businesses can enhance their production efficiency, reduce costs, and ultimately bring better products to market faster.
For more information on prototype mold makers and how they can benefit your business, visit deepmould.net.